ABB125
Established Member
Good morning,
I have recently bought an electronic controller for my model railway.
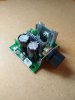
The potentiometer, in its current position, will be relatively awkward to install on my control board (partly because it's hinged). I noticed the white connector next to the fuse, and another potentiometer I have will fit perfectly into it.
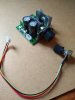
The problem is, I don't know what effect doing so will have. I assume the two potentiometers would be connected in parallel (but I'm not sure), but surely this would create anomalies if both are adjusted (perhaps accidentally). Also, the potentiometer on the board is a B100k, whereas my spare one is B10k; would this cause any issues?
Here is a picture of the bottom of the board. The built-in potentiometer is the three pins between the screws on the right, the white socket is the three pins to the left of the screw hole top right.
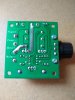
And hopefully you will just be able to make out what looks like a connection from the potentiometer to a resistor on the top.
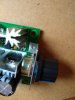
Many thanks for any advice, if you need any more detail please ask.
I have recently bought an electronic controller for my model railway.
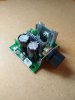
The potentiometer, in its current position, will be relatively awkward to install on my control board (partly because it's hinged). I noticed the white connector next to the fuse, and another potentiometer I have will fit perfectly into it.
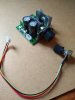
The problem is, I don't know what effect doing so will have. I assume the two potentiometers would be connected in parallel (but I'm not sure), but surely this would create anomalies if both are adjusted (perhaps accidentally). Also, the potentiometer on the board is a B100k, whereas my spare one is B10k; would this cause any issues?
Here is a picture of the bottom of the board. The built-in potentiometer is the three pins between the screws on the right, the white socket is the three pins to the left of the screw hole top right.
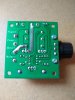
And hopefully you will just be able to make out what looks like a connection from the potentiometer to a resistor on the top.
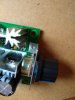
Many thanks for any advice, if you need any more detail please ask.